 |
 |
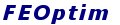 |
The application of FEM-Analysis becomes more and more important in industrial CAE-product development. To support econimical requirements, specialised software packages have to be developed, which will satisfy the benefits of CAE-engineering in regard to short development and production periods.
|
A special appplication in FEM-Analysis, called Structural Optimization, will be an importnat subject in the future. With the aid of structural optimization, the cae-engineer is able to find the best analysis structure concerning optimal structural responses.
In order to support such special cae-problems as
- Short product development periods
- Optimal products
- Simple and efficient application of structural optimization methods
comes the software package FEOptim.
The main purpose of this program is to givethe cae-engineer a powerful tool for creating design models in a simple and efficient manner. The program includes the following optimization related basic features.
- Simple graphic interface
- Powerful 3D-display visualizing analysis-/design model
- Extremely fast inut/output data interfaces to major CAE-programs (MSC/NASTRAN, SDRC/I-DEAS, etc.)
- Fast and efficient handling of large scaled FE-models
- Visualizing of pre-/postprocessing data concerning structural optimization
- Creation of design-models concerning MSC/NASTRAN statement terminology
- Updating of analysis structure with optimized parameters
|
FEOptim - preprocessing phase of design optimization 
FEOptim ofers the CAE-engineer an efficient interafce between FE-Analysis and optimization of FE-structures. The program has the capability to visualize the FE-model in a dynamic 3D-graphics display and to overlay the structure with analysis results (e.g. stresses, displacements). Based on this information, the engineer can interactively create a design model for MSC/NASTRAN, which includes
- Design variables (lower/upper limit)
- Design constraints (lower/upper limit), based on
- Design variable
- Structure property
- Structure response
- Synthetic response
- Design Target Function (min/max Optimium)
This design model created by FEOptim will be output completely in MSC/NASTRAN format (BULK DECK - Design Model). In combination with the analysis model, the user is able to generate an FEM-analysis/optimization job (MSC/NASTRAN - SOL 200) for large scaled FE-models (> 100 000 DOFs) with less effort and without errors.
|
After finishing the analysis/optimization job (MSC/NASTRAN - SOL 200), the user has the problem to control th elarge amount of data (optimization history/result data), which the job will produce. FEOptim reads and stores data in an object related database and is managingthe data interactively by a graphical display user interface.
To control and evaluate the data FEOptm is able to visualize selected optimization parameters as list charts, bar/column charts and graph charts. To reduce th elarge amount of data in an efficient way, FEOptim offers several criterias (e.g. max. component weight, max. shell thickness)
|
FEOptim - Product characteristics 
- SDRC/IDEAS (Universal File)
- MSC/NASTRAN (OP2, XDB, Punch, Bulk, F06)
- CSA/NASTRAN (OP2, Punch, Bulk, F06)
- OSF/Motif 1.2 GUI
- On-line context buttons
- Control tool panels
- 3D - graphics
- SGI (IRIX) - OpenGL
- HP (HP-UX) - PHIX library
- IBM (AIX) - OpenGL
- All Unix-systems with OSF/MOTIF
- Operating system - Unix
- Disk memory: 20-30 MB
- Other platforms upon enquiry
- Automotive
- Aerospace
- Ship building
- Railway
- Machinery
Preprocessing optimization
- Design model (MSC/NASTRAN Bulk Data)
- Implementation of basic FEA-results as designmodel constraints (displacement, eigenvalue, frequency response, acoustic, stresses
- Linking of design variables
- Creation of equations concerning
- Physical properties
- Static responses
- Dynamic responses
- Acoustic responses
- Frequency responses
- Synthetic response (DRESP2)
- Creation of various target functions (Beta-method inclusive)
- Library crossections
Postprocessing optimization
- Optimization history and results (MSC/NASTRAN Punch-, F06-, XDB-File)
- Evaluation of optimization history concerning efficient design variables, properties and responses dynamic linking of design variables to model parameters (weight, volume, shell, thickness, beam properties, etc.)
- Analytical Model Update with optimized parameters
- Visualization of output lists, graphs and bar charts
- Coloured 3D geometric description
- Contour plots
- Animation
- Weight analysis
Sensitivity Analysis to design variables
- Static responses (displacements, stresses, forces)
- Dynamic resonses (eigenvalue)
- Frequency response (frequency spectrum)
- Transient response (time spectrum) - disp, velo, acc, stress, force
|
|
 |